"The big block Chevy is one of the most raced engine platforms in motorsports. We've compiled some history and a massive library of parts swap knowledge into a comprehensive resource. Read on!"
The big-block Chevy goes by many names – the Rat, the Porcupine, and if you go back far enough, the semi-hemi. It started life as a major upgrade from the 348/409 W motor. What eventually became the MKIV first appeared as the Mystery Engine at the 1963 Daytona 500. The debut was both promising but ultimately inauspicious. The Mystery Engine made far more horsepower than its big-block ‘60s contemporaries like the 427 FE Ford, but nearly all failed either in qualifying, practice or the 500-mile race. None finished.
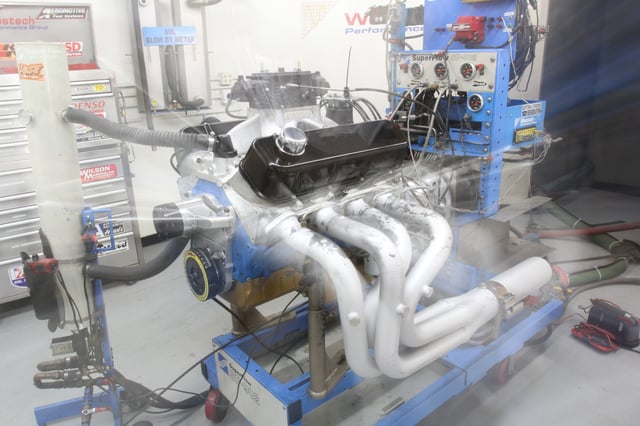
Chevrolet recalled all but a couple of these engines and returned in 1965 with fully developed 396 and 427ci production engines whose present-day versions now are ubiquitous and have pushed the displacement “barrier” far beyond 700 cubic inches. For this story, we’ll concentrate on the production engine lineage of this highly-successful engine family tracing its heritage from the earliest to the most contemporary while offering data on interchangeability.
In fact, this ability to exchange components between displacements that are often separated by five decades of casting dates is perhaps the keynote of both the small- and big-block Chevys. With only a few exceptions, interchanging parts and the huge tonnage of aftermarket parts availability makes the Rat motor a true survivor. While the majority of big-blocks displaced 454 inches, Chevy did build a production engine displacing 496ci. But the future of the Rat appears to be stroker versions and today you could easily build a stock deck height Rat motor at 500-plus-ci using off-the-shelf parts.
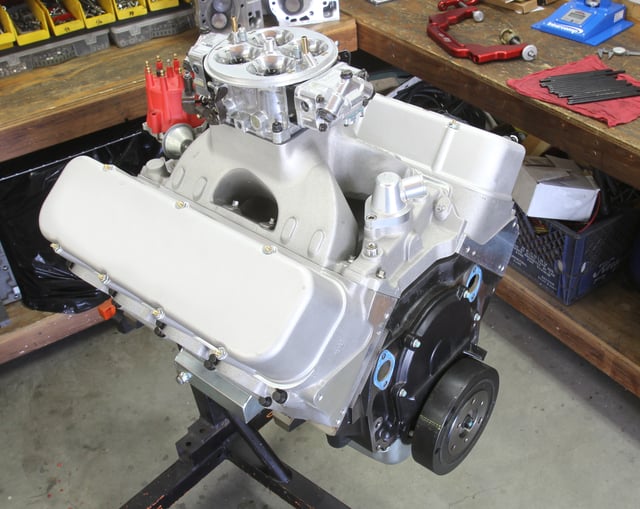
Displacement
The earliest production big-block Chevy appeared as the 396 and bolted into the new-for-’65 full-size Impalas as well as in the Corvette. There were even a precious few ’65 Z-16 SS396 Chevelles built in 1965. This was enhanced in 1966 with multiple horsepower combinations of the 427 as high as 425 horsepower. By 1970, the 396 had grown to 402 inches with a 0.030-inch overbore (although still badged as the SS 396 in the Chevelle) but was overshadowed by the introduction of the 454.
These engines were labeled as Mark IV versions, the fourth in the developmental lineage that could be traced all the way back to the late ‘50s 348/409 engines. In fact, the MK IV shares the same bore spacing and main web position with its W-motor ancestor although the big-block main journal is roughly 0.250-inch larger in diameter. Minor changes to accommodate a one-piece rear main seal and hydraulic roller lifters occurred with the advent of the Gen V and later the Gen VI engines in the 1990s.
Even with Gen V/VI revisions, the 454’s displacement remained constant for decades until GM radically changed the big-block, pushing a production heavy-duty truck engine up to 8.1 liters (496ci) that appeared in 2001. The bore remained at 4.250 but the stroke increased from 4.00- to a hefty 4.37-inches. Unfortunately for interchange artists, GM changed nearly everything in the engine so parts compatibility ended with this 8.1L. It’s better to think of the 8.1L as a completely different engine and not in the same lineage as the rest of the big-block lineup.
Even bigger yet was the 502ci Rat that is worth mentioning even though it never appeared in a production GM vehicle. Sold through Chevrolet Performance, this is a later model Gen VI engine sporting a serious 4.500-inch bore, which opens up great potential for multiple big-inch, bore-stroke combinations.
We’ll decompress the Rat into its major components to give you an idea of how each of these parts fit into the overall big-block chain of displacement and power opportunities. While the small-block Chevy has been overshadowed now by the LS family, the big-block Chevy is still the best approach for building a big cubic inch GM engine for the street.
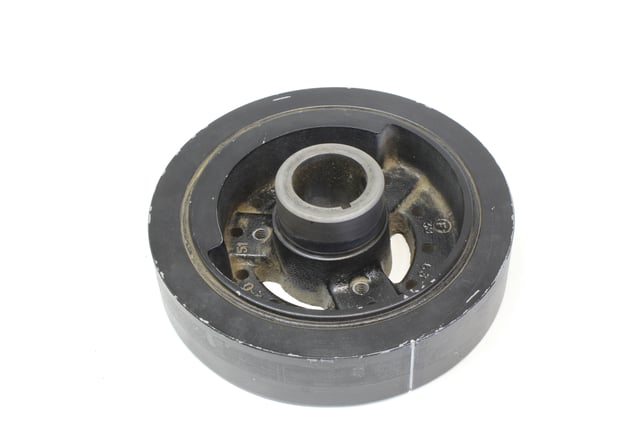
Blocks
The one consistent factor throughout the entire evolution of the big-block Chevy has been its bore spacing. All big-blocks utilize the same 4.840-inches of distance between the cylinder centerlines. This dimension has remained fixed until you get into custom 5.00-inch bore spacing blocks from companies such as Dart Machinery that are most often constructed as pure competition engines. The factory bore spacing is wide enough to easily accommodate 4.50- and even 4.60-inch bores that still create sufficient room between the cylinders for adequate head gasket sealing and engine cooling.
From a production standpoint, GM only built iron blocks with one exception – the 1969 ZL1 427 engine built for the Corvette and COPO Camaros. This was an exotic (for the time) all-aluminum engine and a major departure for GM. Today, the best place to find an aluminum block would be the aftermarket, like Dart. Block technology has improved to the point now where the only barrier to running an all-aluminum Rat would be the cost of entry.
The original MK IV blocks used the traditional two-piece rear main seal technique from 1965 continuously until the Gen V engines appeared in 1991 that moved to the one-piece rear seal configuration. This is one of several big changes for these cylinder blocks with the Gen V and later Gen VI versions in 1996. Along with the rear main, the Gen V modified the head gasket sealing configuration, added hydraulic roller lifers, revised the oil pan gasket to a one-piece, and reconfigured the front timing chain cover bolt patterns.
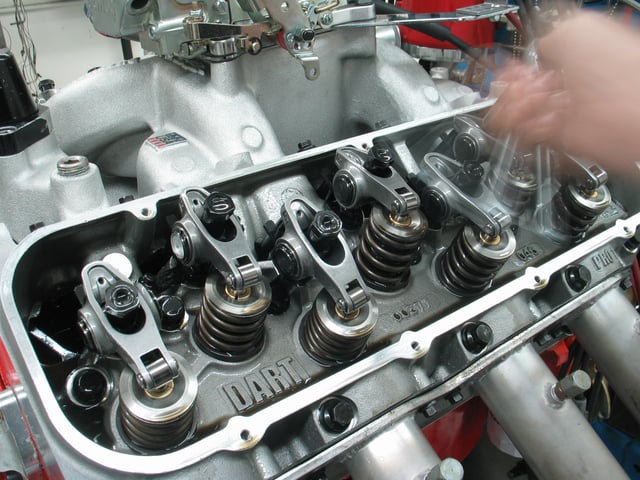
The Gen V conversion to hydraulic roller lifters also effected revisions to the lifter valley with taller cast-in lifter bores needed to accommodate the increased height of the roller lifters. The lifter valley also incorporated a few minor additions of dogbones and a sheet metal “spider” to retain the lifters that we’ll illustrate in the accompanying photo.
The good news is that these later blocks maintained the original block deck height, bellhousing and motor mount bolt patterns so swapping between older and newer generation blocks is relatively simple. There are some minor differences, however. The Gen V production blocks were designed for EFI induction systems so the Gen V production blocks did not include a mechanical fuel pump boss nor the cast-in location for the stock cross-shaft for mechanical clutch linkage. If these are critical, aftermarket versions of these blocks are available from Dart that easily accommodate these additions.
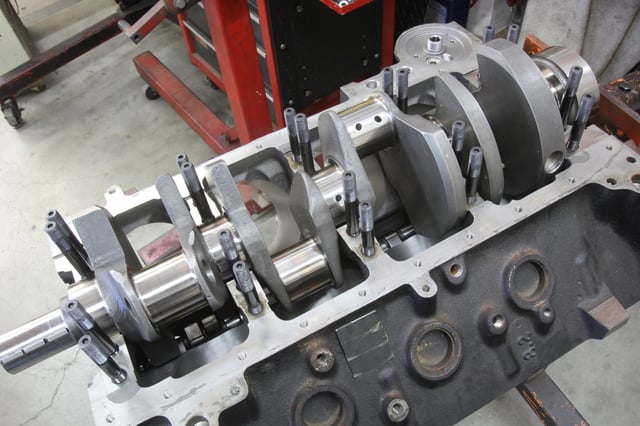
A major Rat motor benefit is its cavernous crankcase that can easily accommodate big stroke increases with virtually no block modifications. This happens to be a 4.50-inch Gen VI block being fitted with a 4.250-inch stroke crank to build a 540.
Crankshafts
Factory crankshafts were offered in both cast and forged versions although cast versions are clearly the most common. All the early 1965 through 1969 engines were also configured as internally balanced engines. This means that both the harmonic balancer and flywheel/flexplate were neutral balance.
This changed in 1970 with the 454 as Chevrolet moved external offset weight to both ends of the crankshaft. This means that these externally balanced cranks required a flywheel/flexplate and harmonic balancer fitted with offset weight in a specific location. These components must not be interchanged with the internally balanced components.
Furthermore, when GM created the Gen V, one-piece rear main seal block this demanded a different crankshaft rear main seal. Since the offset flexplate/flywheel mounting flange could no longer accept that small offset weight, the external balance number for the flexplate/flywheel increase from the 2-piece rear main seal’s 33 ounce-inch (oz-in) value to the Gen V value of 42.5 oz-in.
It’s critical to know which internal or externally-balanced engine you have when adapting big-blocks to different vehicles because of these differing external balance values. Making all this even more potentially confusing is that within these three different flexplate/flywheel combinations the crankshaft bolt pattern remains the same. So just because the flexplate/flywheel bolts to the engine doesn’t mean the correct wheel is in place.
Connecting Rods
The connecting rod story is thankfully far less convoluted. There are basically two main factory connecting rods and the difference really comes down to rod bolt size. There are many other minor differences, but the first big-block 6.135-inch length versions were fitted with 3/8-inch rod bolts. The major upgrade soon followed with high performance 396 and 427 and all subsequent performance engines using a 7/16-inch bolt. Most production big-block rods were of the pressed-pin variety meaning that the wrist pin was pressed into the small end of the connecting rod. But even some early performance engines switched to a full floating arrangement with a bushing in the small end of the rod.
In mild performance applications, stock rods do a fine job. But in a serious application where engine speeds exceeding 6,500 can be expected, an aftermarket 4340 forged steel I- or H-beam rod is a prudent investment. Rods don’t make horsepower, but a failed rod can cause catastrophic damage and is hardly worth the risk. By the time a stock rod is Magnaflux tested for cracks, shot-peened, new ARP rod bolts fitted, and resized – that investment is not far from the cost of a much stronger set of aftermarket rods.
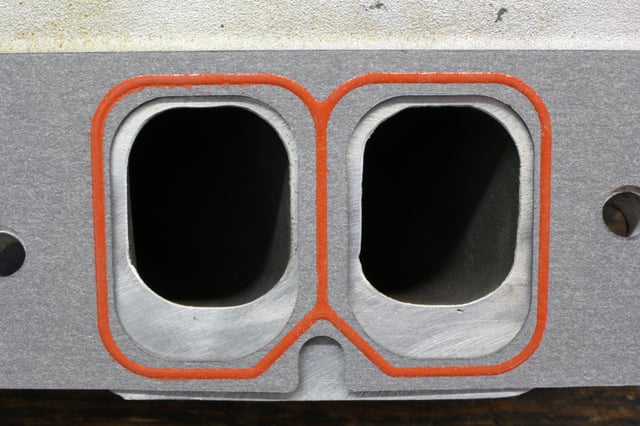
Cylinder Heads
Over the decades, the big-block has experienced a raft of various production cylinder head variations. The earliest heads came in both cast iron and aluminum but employed what is now called a closed combustion chamber. The tight chambers shrouded the small valves and by 1970, second generation heads were blessed with a larger, open chamber construction that allowed up to 2.250-/1.88-inch valves.
While combustion chamber size and configuration is important, most enthusiasts tend to focus on intake port configuration. Here, Chevrolet offered two variations –oval and the rectangle. Oval port heads were aimed at base engine packages while the rectangle port heads were reserved for the performance engines. Later, some heavy-duty truck engines were fitted with what are now called peanut port heads which is a clue as to their miniscule inlet opening.
The best of the iron oval port, open-chamber heads are the casting number 353049 versions that when upgraded with larger 2.25-/1.88-inch valves and some very minor port work can deliver impressive power. Of course, the down side is that they’re massively heavy. Most performance seekers will opt for any number of aftermarket aluminum heads like those from Dart. There are various chamber, valve, intake runner, and valve spring options that will fit nearly any application.
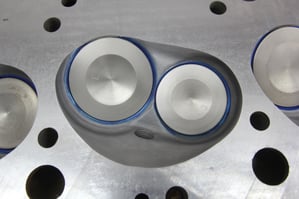
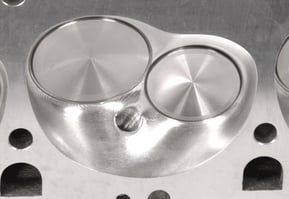
In terms of interchangeability, the biggest concern is chamber compatibility with the pistons and ensuring the compression ratio meets your needs. One thing to keep in mind is that closed chamber heads cannot be used on an engine with domed, open chamber pistons because the dome will physically hit the head. This isn’t a concern with flat top or dished pistons but is a hard and fast rule with domed pistons. Conversely, a domed closed-chamber piston engine can accept open chamber heads without interference.
The difference in chamber size can push the compression in an unintended direction if not matched properly so that’s an area to keep in mind. For example, tossing a set of 454 open-chamber heads on a 396 could radically reduce the compression ratio because of the roughly 10cc larger chamber on a short-stroke engine.
Camshafts
Production big-blocks all the way into the mid ‘90s were always flat tappet camshaft engines. When GM converted to the Gen V, the big change was fitting the new big-block with hydraulic roller lifter camshaft. This was mainly aimed at reducing engine friction that promised better fuel mileage. At first the hydraulic roller was scoffed at, but today’s high quality lifters can now deliver on serious 700 to 800 hp packages using an improved version of these original hydraulic rollers.
This move not only changed the style of the lifter but also how the cam was retained. When converting flat tappet big-blocks over to a roller requires the use of a button that contacts the inside timing cover to prevent the cam from moving forward. Gen V and VI engines use a steel retaining plate over the cam which requires a stepped nose on the camshaft and a different cam gear.
This move to hydraulic rollers also made a change to the rocker arm assembly. From the earliest days, big-blocks like their small-block cousins were fitted with individual stud-mounted rockers that required adjusting the installation preload. The factory hydraulic roller lifters also converted to what is called a net lash system where a rocker arm bolt tightens the stamped steel rocker in a set position. This design uses pushrod length to set the proper lifter preload. There are kits available to convert these heads over to adjustable roller rockers.
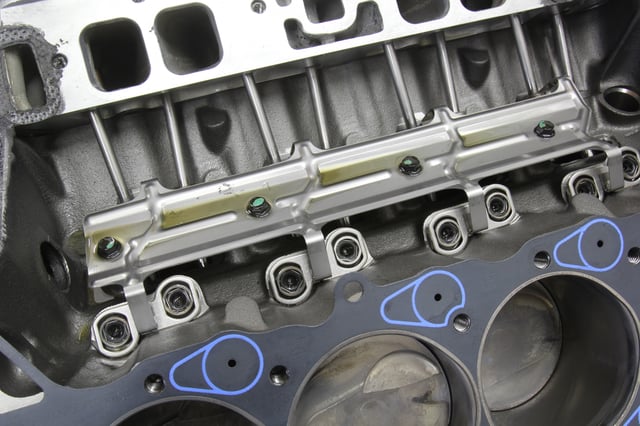
Intakes
With both oval and rectangle port big-block cylinder heads, this dictates that the intake manifold port must also match the cylinder head port configuration. The bolt pattern between these two heads are the same, so in a pinch it is possible to run an oval port manifold on a rectangle port engine and, contrary to what most forum experts will proclaim, there really isn’t a major performance degradation.
Production big-block intakes are, for the most part, uninspired but the aftermarket has you covered for either oval or rectangle port engines in both dual plane and single plane versions.
Conclusion
In the interest of brevity, this effort has just covered the crest of the monster wave of data available for production big-block Chevy street engines. Opportunities abound to build a big cubic inch street motor that even normally aspirated has the grunt to make an impressive street engine.