Making the jump to an aftermarket Dart block comes with a host of performance benefits. One of the biggest, in terms of durability, is stepping up to a priority main oiling system. Read on to learn exactly what that means.
In a priority main oiling system, the oil from the engine’s primary oil gallery is supplied first to the main bearings and then to the cam, lifters and top end. The bottom end of a performance engine can generate high levels of heat. In highly stressed racing applications, priority main oiling ensures that the critical crankshaft main bearings and connecting rod bearings receive adequate lubrication. A steady supply of fresh, clean oil helps to keep the temperatures down and greatly increases the longevity of the bearings and associated components.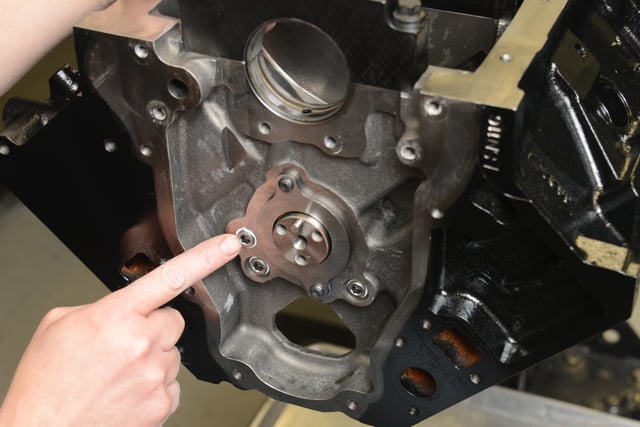
Factory vs aftermarket oiling
For a closer look at how specialized aftermarket engine blocks from Dart Machinery differ in their oiling schemes to regular factory blocks, we spoke to Kyle Scheel, aDart Sales and Technical Representative who’s been around vintage cars and motorsports his whole life.
“Factory engine blocks that are not designed for the demands of racing do not incorporate priority main oiling,” he explains. “They typically oil from the top end down, feeding oil to the top end first as it is easier to machine them in this fashion. In that scenario, the lifter gallery actually serves as the main oil gallery.
“This places a much greater demand on oil volume but is great at keeping the valvetrain lubricated and quiet. What is not great is that the rods and main bearings are oiled secondary, which poses a serious threat to engine life in performance applications. The critical rod and mains may be starved of oil, overheat, prematurely wear, and ultimately lead to engine failure.”
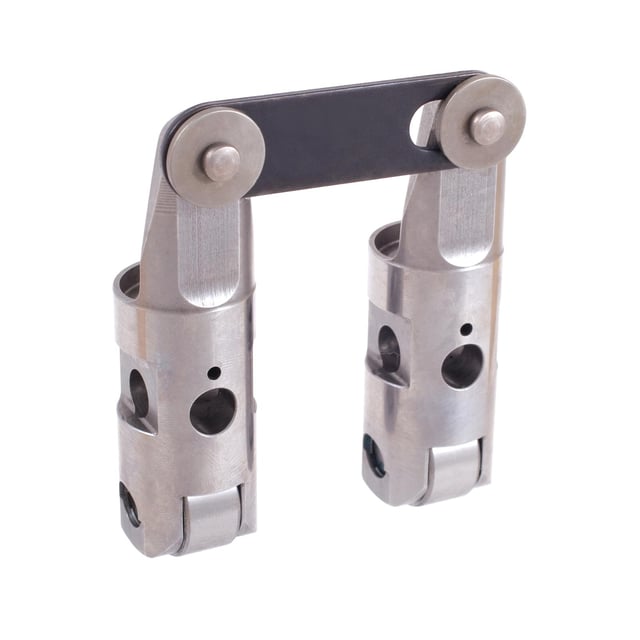
By contrast, all Dart Machinery engine blocks have upgraded priority main oiling systems.
“Oil volume demands are reduced, and the most critical areas of the engine are provided with the best level of protection first,” adds Scheel. “Also keep in mind that priority main oiling is not detrimental to the upper engine components or valvetrain as their oiling needs are much less.”
Trends in engine oiling
Babbitt-type bearings are constructed of multiple layers of different metals and often feature a protective coating. Bearings have a smooth, flat surface onto which oil is pumped to reduce friction against a spinning journal – crank, rods, cam. The spinning journal rides on a hydrodynamic ‘wedge’ of oil, not directly on the bearing material.
According to Jeff Lake, Dart’s resident engine builder with over 35 years of experience, improved oil technology is having a big impact on trends in engine oiling.
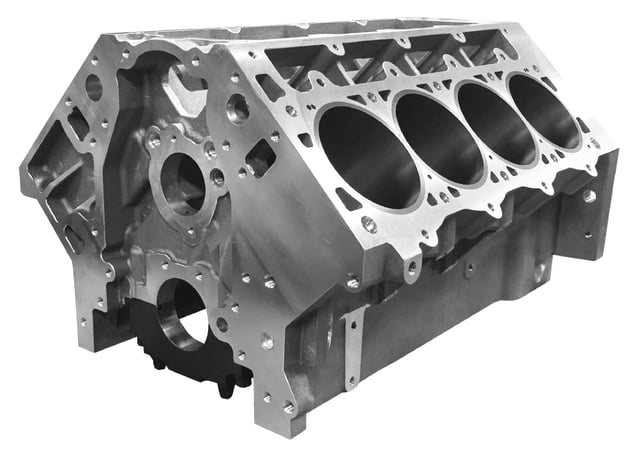
“Oils are better than they have ever been,” he says. “Conventional wisdom in regard to bearing clearances that ‘loose is fast’ is giving way to a new line of thinking. Engine builders are running tighter bearing clearances with modern, thinner oils that can stand up to the abuse of high-performance engines. With thinner oil you can move more oil volume with less effort. Additionally, the thinner oil creates less friction as it moves through the oil passages inside the engine and therefore less heat is generated in the oil.
“In the past, the theory was that a heavier weight oil like a 20W50 would stand up to the abuse in a racing application, provide more cushioning to the parts, which were looser for less drag,” Lake continues. “Now, it’s not uncommon to see zero-weight oils and really tight clearances.
“The bearings, too, have developed hand-in-hand with the thinner oils. The likes of Clevite, Dura-Bond or King all have their proprietary takes high-tech, hard-wearing, super-slick coatings. These used to be reserved for very high-end racing, but are now on almost all bearings.”
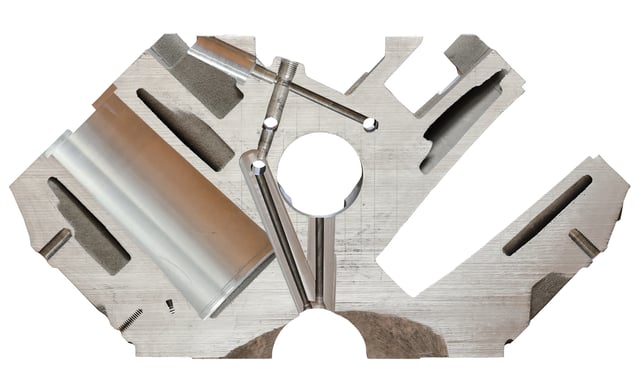
Targeted changes
All of Dart’s blocks are brand-new production items to the engineers’ own designs – nothing is remanufactured or modified. Material is added in a variety of spaces. Cooling jackets are reworked and expanded for example, and cylinder-wall and deck thicknesses are increased. The key factory bore spacing, lifter bore locations and angles, deck height, engine mounts, bolt patterns and accessory bolt holes are all retained.
The nature of the changes that Dart makes to improve upon factory designed oiling systems varies by manufacturer and block type.
“Factory Ford (Windsor block family) and Chevy (big block and small block) engines are all different in the volume of oil they can move and the volume of oil they really need in the different areas of the engine,” says Scheel. “As a result, changes we apply in our blocks are not one-size-fits-all.
“In general, we make sure that our blocks oil the bottom end first (priority main) and with an adequate amount of oil. We may also reduce oil gallery diameters to add strength back into the block while not hindering the volume of oil that can flow through it.
“Additionally, we look very closely at the location and placement of the lifter galleries to be sure that they will allow for raised camshaft locations and larger-than-stock camshaft diameters,” he continues. “Raised cam locations and larger cam cores are very popular upgrades. Most of the time the factory lifter gallery locations will not accommodate those upgrades.”
Dart will also add or eliminate oil crossovers in the lifter valley at the front and rear of the block, as is appropriate to meet the oiling requirements. Along with crossovers, Dart adds provisions for oil restrictors that enable the oil volume being sent to the top half the engine to be reduced and fine-tuned, while maintaining full volume to the rods and mains.
“Finally we add front and rear external oil feeds for external oil pumps and oil accumulators,” Scheel notes. “The customer can deploy a traditional wet-sump setup with the pump in the pan, a wet sump with an external pump, or a dry sump with an external pump. This makes our blocks very versatile and they can easily find a home in any application.”
Total control
With the exception of mixing and pouring the metal, which is handled by external casting specialists using designs and tooling under Dart’s control, the entire block development, production and finishing process is completed in-house. More than 30 machining centers run 24 hours a day for 6½ days a week to keep up with demand.
This production setup means that Dart can closely control quality, accommodate customer requests, and continuously participate in R&D.
Future improvements to internal components and further advances in oil technology will certainly impact the oiling features of Dart blocks, which will continue to evolve. The company remains watchful of, and responsive to, new technology as it becomes available.